Any typical industry today comprises many processes with different complexity. These processes can be broadly divided into five logical levels. This categorization is done based on the nature and complexity of industrial processes. Although there is a lot of overlap between processes nowadays, the fundamental activities at each level remain the same. This can be visualized as a pyramid as shown in the image below. This is called as Industrial Automation Pyramid.
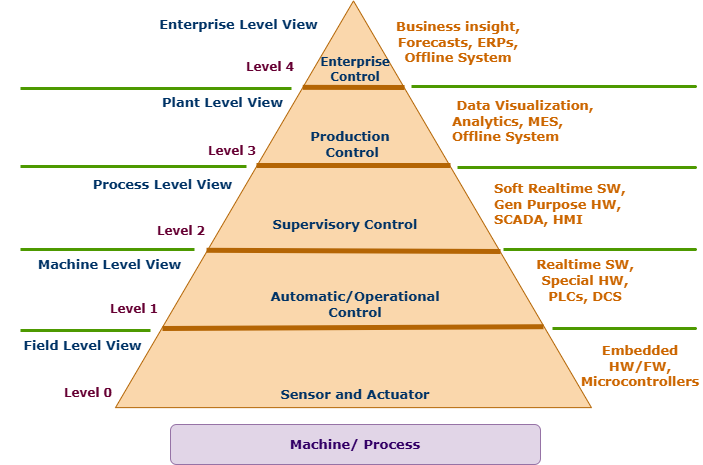
Level 0: It gives a field-level view. This level directly works with machines operating on the floor shop. Sensors and Actuators are like the eyes and arms. One sensor just works with one variable. For example, a temperature sensor senses the temperature at one location. If there is a need to measure the temperature at multiple locations, many sensors have to be deployed. Similarly, one actuator controls one parameter alone.
Level 1: It gives a machine-level view. A machine performs one unit of a task. For example, at a typical manufacturing shop floor, there are machines to perform tasks such as milling, grinding, drilling, cutting, etc. There are specialized controllers to control all functions of the machine as a single unit. These controllers internally use information captured by sensors and actuators to perform the task. In manual operation, an operator typically operates one machine and performs one task at a time.
Level 2: It gives a process-level view. It’s an aggregate of tasks performed by individual machines at Level 1. Several machines performing their tasks in a sequence to achieve an output. For example, a block of steel will undergo several processes to take the shape of a gear. The outcome will be the final product or an unfinished component.
Level 3: It gives a plant-level view. The typical plant consists of several processes such as raw material handling, machine job, paint shop, packaging, etc to convert raw material into a final product. In some cases, raw material could be components that are assembled into the final product.
Level 4: It gives an enterprise-level view. It’s a top-level view that oversees and manages the complete business. Operations like manufacturing, sales, purchase, finance, and payroll come under this level.
Flow of Information
All levels are interconnected with the industrial communication system. When we go from level-0 to level-4, information gets aggregated. The level-0 and level-1 are time-critical activities. It’s a hard real-time system. Events and their response must happen in the allotted timespan. Response time is less than a second. Level 2 operates in a soft real-time manner. It has to complete under the allotted time slot but response time is not as stringent as level-0 or level-1.
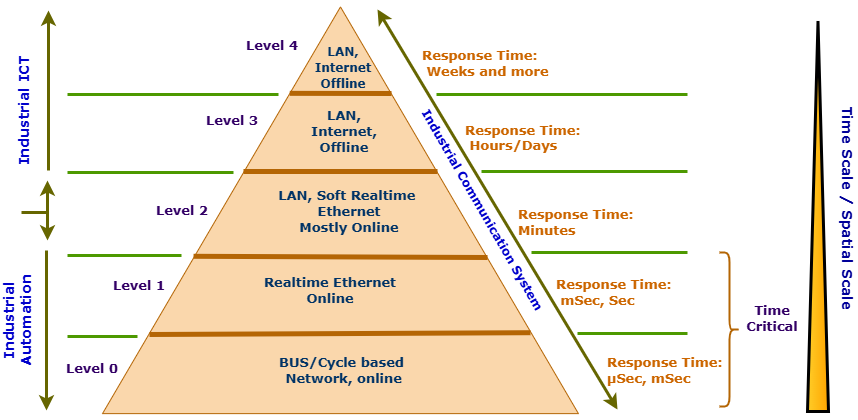
Processes involved in the lower three levels come under industrial automation. The top two levels come under information and communication technologies(ICT).
There are many mature and robust applications, tools, and technologies to automate manual operations at all levels of any manufacturing industry. A discussion of individual technologies is out of the scope of this article.
Roadmap for Automation
Complete automation of any plant or factory or office cannot be done in one or two quarters. First, an automation roadmap has to be prepared. In the first stage, non-critical processes can be automated. Measure the benefit observed from automation. Then go for the next stage of automation. Automation includes training and skill enhancement of the existing workforce.

Data collected from the bottom level is processed and analyzed by its next upper level. Processed information trickles up to the management. This is one of the benefits of automation. Accurate data from each level can be collected. This can be visualized and analyzed to derive business insight.
Without basic automation, the Indian manufacturing industry can not adopt and benefit from advanced solutions such as Industry 4.0, predictive maintenance, and AI.