Data Acquisition devices are used to collect physical condition data. This data is used for IIoT, Industry 4.0, and compliance purposes. Physical condition data comes from multiple sources:
Process data from plant and machinery: Temperature, Vibration, Pressure, Speed, System uptime amp; downtime, Fuel level, etc
Physical Environment: Noise, pollution level, Humidity, Temperature, Liquid level, Light intensity, etc
The data is collected using various sensors. Industrial equipment such as SCADA, PLCs, energy meters, etc generates various data points. Data is received in both analog and digital formats. DAQs process collected data and send them to the computer system for industrial and scientific usage.
Modern DAQs are full-fledged systems consisting of HW and software applications. The software includes a dashboard to visualize the data received from HW. Various communication interfaces are included to handle data from multiple sources. With automation and Industry 4.0 taking center stage in the current industrial setup, the role of DAQ has increased manifold.
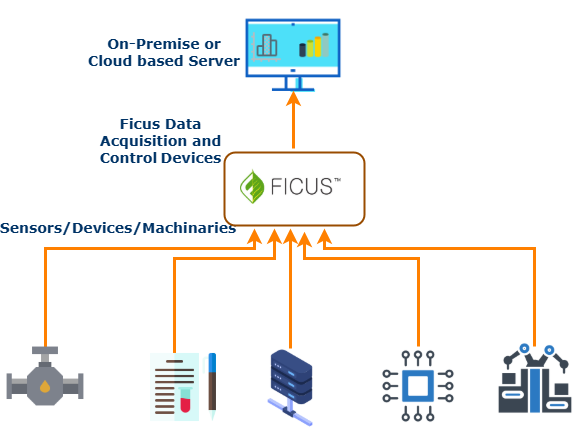
DAQ Design Consideration
The design and architecture of DAQ differ depending upon the application. Some important considerations:Type of data being collected: Physical property of the system being measured.Sensors being attached to it: How many sensors of what type are being connected to DAQ? External or internal sensors, the power source of sensors.Storage Media: RAM, EEPROM, USB, amount of storage, memory management.Data communication: Wired or wireless communication, different communication protocolData processing or filtering: Does data need some local processing or filtering, the microcontroller used, etc.Power source: Battery, AC, or DC supply.Usage: Use cases. Based on this, the enclosure or external packaging of the DAQ will be designed.The DAQ manufacturers need to design the system taking the above points into consideration.
DAQ Block Diagram
The diagram below gives a high-level view of DAQ. Detailing each step of data acquisition electronics is out of the scope of this article. Electronic Components such as multiplexers, Sample-Hold, Anti-Aliasing Filters are used in various combinations depending upon the architecture of DAQ. Many of the components are not shown for the sake of simplicity. Analog signals can be used directly for any practical purposes. Signals captured by sensors from the physical system or machinery are often weak and full of noise. Signal processing techniques are used to process and make them useful. This is done with the following methods:Signal Processing or Conditioning: Performs amplification, isolation, filtering, and linearization on the input signal.Analog to Digital Conversion: Converts analog signal into digital format.DAQ must read the signal at the right sampling frequency. The incorrect sampling rate may introduce low-frequency errors which will distort the original signal. Controllers used in DAQs are either: Microcontrollers: Common Industrial and commercial use cases.FPGA: High-end use such as Defence and critical scientific use cases.
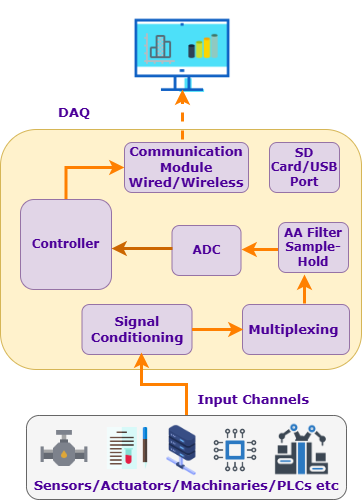
Data Acquisition Setup
Capturing industrial data is the first step in the automation process. Industries that are going for automation and Industry 4.0 must plan and decide their data strategy. Stakeholders must devote some time to identify and select critical data points. Once, data strategy is ready, set up the correct infrastructure to collect and acquire data points. Data has to be adequate and accurate. Data accuracy is not possible without the correct design and implementation of data acquisition infrastructure.
Summary
A wide variety of DAQs is available catering to all types of requirements. Industries can procure standard DAQs off-the-shelves which are adequate for most of the common use cases. DAQ manufacturers can manufacture customized DAQs as per the applications requirement. A well-planned data strategy along with robust and accurate data acquisition infrastructure will help industries achieve their Industry 4.0 goals.